Organizational Alignment: How to Do It and Why It’s Important for Facility Managers
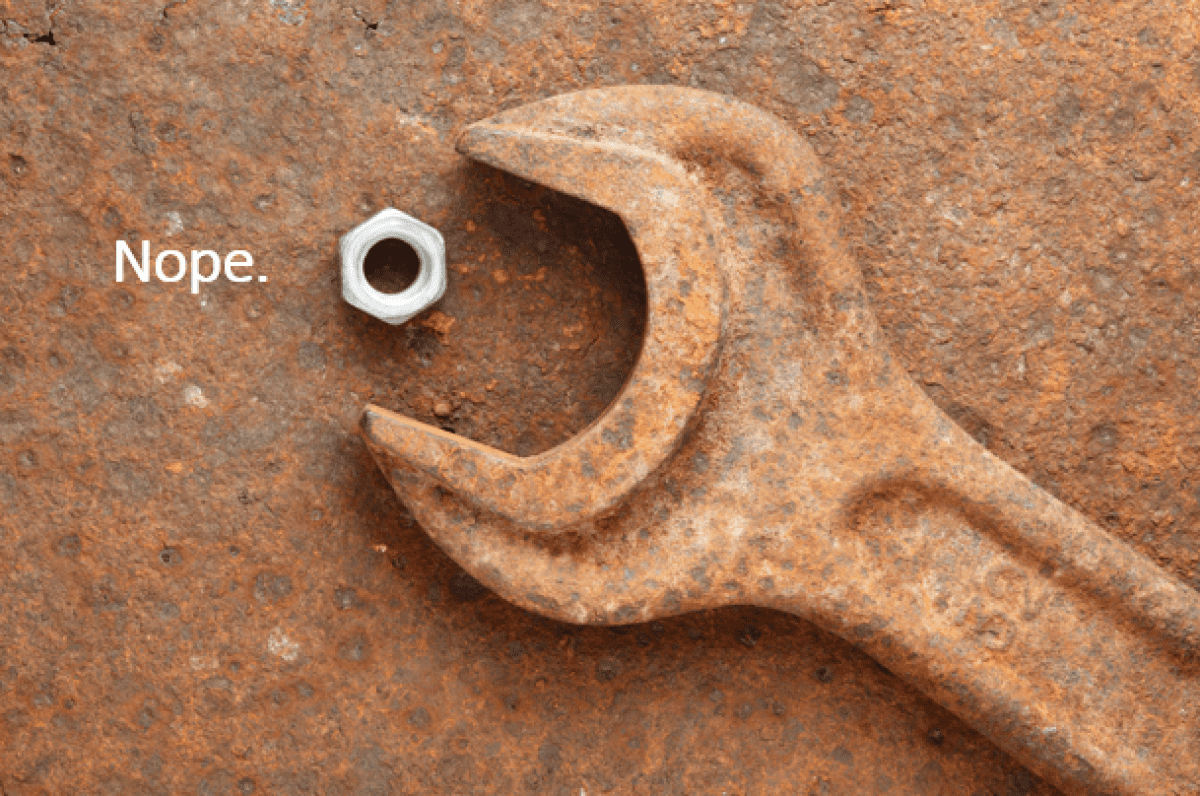
Organizational alignment is the process of aligning human capital and staff development with an organization’s strategic goals. In facility management, these goals could focus on reducing operating costs, improving energy efficiency, completing large capital projects for future growth, or improving regulatory compliance and life safety. Whatever the organization’s goals, it’s critical the right resources are used to attain them.
Organizational alignment starts with benchmarking. Using a preferred benchmarking tool or consultant, evaluate the organization’s current O&M resourcing portfolio (i.e. staff and cost mix of insourcing and outsourcing). A balanced portfolio is one which the sum of its labor costs and service contracts is near or at the 50th percentile of its national peer group. Even if labor costs are high or low comparatively, that’s not as important as the sum. It’s to be expected that an organization with a high internal labor cost will incur lower costs attributable to service contracts and external work orders (and vice versa).
If the sum of the two parts is approximately the same as (or better than) the mean of the peer group, then the organization is likely performing well in this area. In addition to staffing and service contracts, benchmarking should address utility costs and material/repair costs since these line items are directly related to labor. Leadership, especially those working within critical environments like hospitals, should also evaluate compliance levels with respect to codes, standards, and regulatory authorities.
Once current performance is benchmarked, the next step is to review and update job descriptions, core competencies, and compensation ranges. Facility management leadership should develop a plan with human resources and other key personnel to reallocate staff to meet these revisions. The results from the benchmarking analysis will inform the optimum staffing level for each skilled trade.
It’s one thing to have all the right people on the bus. It’s another if they’re all sitting in the right seat.
Benchmarking results can be deceptive, which is why it’s important to find a tool or consultant that considers staffing by trade/craft. The overall staffing budget might be within the acceptable range, but this doesn’t necessarily mean an appropriate skill mix is utilized to address maintenance schedules and repairs. Again, this is why service contracts and outside contractor expenses are evaluated and not just in-house staff.
If the overall staffing level must adjust up or down, consider cross-training staff so they learn skills beyond their traditional trade scope. In recent years, facility management has trended toward a zone technician or general maintenance technician model which a single FTE might assume responsibilities from multiple crafts. This trend is largely in response to the need to reduce operating costs and the increasing role of technology in facility management.
Next, develop a crosswalk from here (the status quo) to better (strategic goals). The crosswalk should include a succession plan and a professional development program specific to the facility management team. If you don’t know where to begin, check out this article on 6 key considerations when developing an internal O&M training program.
The overall objective is to sustain the balance achieved during the organizational alignment process. It’s likely the revisions to job descriptions and staffing levels resulted in some gaps within the O&M department. Use succession planning as an opportunity to fill these gaps and develop a strategy to develop and train the team going forward. Revisit this strategy annually as strategic goals within any organization are likely to change and evolve over time. The same point applies to staffing – people come and go, so have a plan in place to address these changes as they occur.
Finally, as the professional development program and other training is implemented, create a resource library to capture valuable materials and content. As new hires are onboarded or as individuals are promoted, this library will prove beneficial to those seeking to refresh or cultivate their skill set. Content could include operation and maintenance manuals, training handouts, relevant codes, guidelines and handbooks, videos and audio recordings, photographs and screenshots, etc. To the greatest extent possible, keep electronic copies of these resources so they can all be saved in a single repository on the organization’s server. A central, electronic resource library is key. Speaking from experience, you don’t want to discover (usually when it’s too late) that the exact resource you need is saved locally on someone else’s drive.
Once the organizational alignment process is initially completed, it’s just maintenance from there on out. Staff are assessed against the core competencies annually, and new hires are evaluated against the same metrics for consistency. The resource library expands over time. Benchmarking is performed once a year to measure performance year-over-year and verify the O&M budget is appropriately allocated.
Simple, right? So, what are you waiting for?
About me: My career has offered me a whirlwind of opportunity in the engineering and construction industry, but my passion is rooted in developing and implementing training programs for facilities management teams. Every facility manager I have ever had the privilege of meeting simply wants to do good work, and my mission in life is to empower them to do more of it.
I have been responsible for the development and management of over $370 million in specialized energy solutions and infrastructure projects. Since starting my career in healthcare engineering consulting, I have provided healthcare facility managers with the tools and resources they need to make data-driven, well-informed decisions that improve their energy efficiency, building performance, and facility operations. The most recent of these solutions is a healthcare facilities operation and maintenance training program, the first of its kind in the industry.
Let’s connect: If you have a success story in facilities management, I’d love to hear about it and learn how you made it happen.